The design team at Sunshar is comprised of experienced designers and modelers proficient in CAD/CAM/CAE software including Unigraphics, Catita, Pro/Engineer, Power Mill, Mold Flow Analysis, and AutoCAD. Our engineers interact directly with the customer and our manufacturing team to identify the best strategies, methodologies and cost-effective designs to manufacture quality components economically.
Solid modeling for...
- Product Design
- Tool Design
- Interference Checking
- Engineering Analysis
- Rapid Prototyping
- Part Print Creation
- Mold Flow Analysis
- Hot Runner system
- Gas assisted injection mold
|
|
Product and Moluld design wiith the latest software technology:
- unigraphics
- SolidWorks
- Creo
- Moldflow
- AutoCAD
|
Software being used for Toolin manufacturing, and to generate cutter paths for CNC machines include:
|
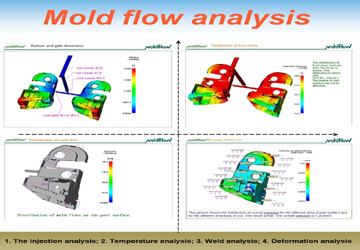 |
Design for Manufacturing (DFM)
Sunshar's design and advanced product development teams are experts at converting your innovative concepts into efficiently manufactured plastic products. With over 10 years industrial design capability, would help our customers from raw material choosing to tooling design and secondary processing to shortens product development time, minimizes development cost, assure the quality, reliability, safety and ensures a smooth transition into production for quick time to market. |
The key should be considered on Design:
-
Understand manufacturing problems/issues of current/past products
It is very important to use specific design guidelines for parts to be produced by specific processes such as welding, casting, forging, extruding, forming, stamping, turning, milling, grinding, powdered metallurgy (sintering), plastic molding, etc.
-
Design parts with symmetry.
Design each part to be symmetrical from every "view" (in a drafting sense) so that the part does not have to be oriented for assembly. In manual assembly, symmetrical parts can not be installed backwards, a major potential quality problem associated with manual assembly. In automatic assembly, symmetrical parts do not require special sensors or mechanisms to orient them correctly. The extra cost of making the part symmetrical (the extra holes or whatever other feature is necessary) will probably be saved many times over by not having to develop complex orienting mechanisms and by avoiding quality problems.
-
If part symmetry is not possible, make parts very asymmetrical.
The best part for assembly is one that is symmetrical in all views. The worst part is one that is slightly asymmetrical which may be installed wrong because the worker or robot could not notice the asymmetry. Or worse, the part may be forced in the wrong orientation by a worker (that thinks the tolerance is wrong) or by a robot (that does not know any better).
So, if symmetry can not be achieved, make the parts very asymmetrical. Then workers will less likely install the part backward because it will not fit backward. Automation machinery may be able to orient the part with less expensive sensors and intelligence.
In fact, very asymmetrical parts may even be able to be oriented by simple stationary guides over conveyor belts.
-
Design for fixturing.
Understand the manufacturing process well enough to be able to design parts and dimension them for fixturing. Parts designed for automation or mechanization need registration features for fixturing. Machine tools, assembly stations, automatic transfers and automatic assembly equipment need to be able to grip or fixture the part in a known position for subsequent operations. This requires registration locations on which the part will be gripped or fixtured while part is being transferred, machined, processed or assembled.
- Minimize tooling complexity by concurrently designing tooling.
Use concurrent engineering of parts and tooling to minimize tooling complexity, cost, delivery leadtime and maximize throughput, quality and flexibility.
- Specify optimal tolerances for a Robust Design.
Design of Experiments can be used to determine the effect of variations in all tolerances on part or system quality. The result is that all tolerances can be optimized to provide arobust design to provide high quality at low cost.
- Specify quality parts from reliable sources.
The "rule of ten" specifies that it costs 10 times more to find and repair a defect at the next stage of assembly. Thus, it costs 10 times more cost to find a part defect at a sub-assembly; 10 times more to find a sub-assembly defect at final assembly; 10 times more in the distribution channel; and so forth. All parts must have reliable sources that can deliver consistent quality over time in the volumes required.
The Rule of 10
Level of completion Cost to find & repair defect
the part itself X
at sub-assembly 10 X
at final assembly 100 X
at the dealer/distributor 1,000 X
at the customer 10,000 X
|